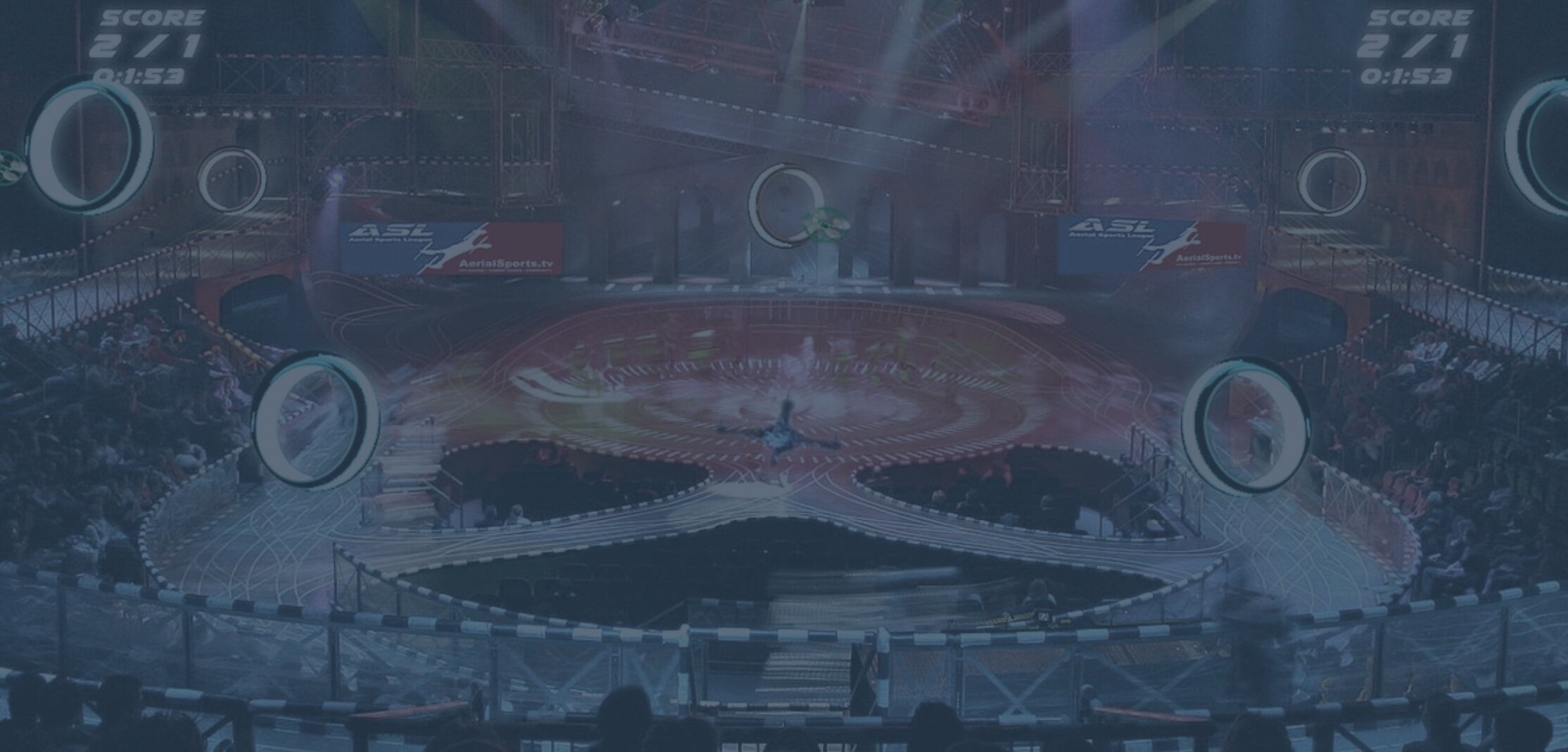
Art to Part < 2 Weeks
The Story
Aerial Sports League, located in San Francisco, was establishing itself as one of the leading racing drone leagues in the United States. Their founding members had been working hard to build a loyal community, and even though they were making strides, they knew they had to do more to assert their presence in the industry.
They wanted to develop a hard, impact resistant drone with a sleek aerodynamic design -- one that was cost effective and easy to maneuver -- which would carry the first “Aerial Sport League Certification” stamp. They wanted to use the drone as a key stepping stone to standardize the racing drone community, placing themselves as a leader in the drone racing community.
Maker Faire, San Francisco, was only 2 weeks away and they realized it represented an immense opportunity to get product feedback from their pilots and sell their vision. They sought out Rapid TPC with an incomplete design and a determination to achieve their goals.
The Solution: Quick-turn
Rapid TPC quickly stepped up to the plate. They met with Aerial Sports League representatives, investigated to their needs, presented a proposal and made an agreement to deliver production samples before Maker Faire.
In less than 2 weeks, Rapid TPC completed the design, chose an optimal composite material and stackup, designed the tool and outsourced its manufacture to an entrusted partner, produced the parts with their automated technology, trimmed the flash, drilled the holes and delivered ready for production samples to their customer, all in time for Maker Faire.
Day 1-3: Design
Following our agreement, the Lead Project Engineer's (LPE) design skills are deployed. He works closely with the ASL lead engineer to listen to his needs and optimize the design and aesthetic of the product.
Day 4: Materials and Stackup
The LPE teams up with the Materials Specialist (MS) to pick an impact resistant composite material and design 3 to 5 composite stackups that would satisfy the part’s strength to weight requirements.
Day 5: Tooling
The LPE and MS complete the design of the tool, receive an RFQ from an experienced machine shop, place an order and expedite the machining job. They also work on custom trimming jig designs, ensuring all features are well aligned.
Day 8: Molding
The tool arrives and the composite stackups are ready for manufacturing. Rapid TPC utilizes an expansive database of forming recipes to tweak the optimal parameters for part quality. The first prototypes are produced.
Day 10: Shipping
The final production samples are trimmed and ready for shipment.